How does the CNC control system determine which tool to select for a specific machining operation?
The CNC control system determines which tool to select for a specific machining operation based on the instructions provided by the operator or programmed into the system.
Here’s an overview of how the CNC control system determines the tool selection:
Programmed Tool Information: The CNC control system relies on a program that contains the instructions for the machining operation. Within the program, the tools and their corresponding tool numbers or identifiers are specified.
Tool Table: The CNC control system maintains a tool table or tool library that associates tool numbers or identifiers with specific tools. The tool table includes information such as tool diameter, length, type, and other relevant parameters.
Tool Call-Up: When the CNC program reaches a point where a tool change is required, the control system refers to the tool number specified in the program. It looks up the tool table to retrieve the corresponding tool information.
Tool Availability: The control system checks the tool magazine or tool storage to ensure that the required tool is available. If the tool is not present in the magazine, an error or prompt may be displayed, indicating that the tool needs to be loaded.
Tool Change Sequence: If the required tool is available, the control system initiates the tool change sequence. It moves the machine to a designated tool change position away from the work area, ensuring safety during the tool change process.
Tool Selection and Installation: The control system commands the automatic tool changer (ATC) to select the designated tool from the tool magazine. automatic change tools cnc router manufacturer The ATC positions the new tool in the spindle and securely clamps it in place.
Tool Length Compensation: Some CNC systems incorporate tool length compensation features. The control system may automatically adjust the Z-axis position based on the tool’s length, ensuring accurate machining based on the tool’s geometry.
Machining Resumption: Once the tool change is complete, the control system moves the machine back to the work area, taking into account any tool length offsets if applicable. It resumes the machining process using the newly installed tool.
It’s important to note that the specific steps and terminology may vary depending on the CNC control system and the machine manufacturer. However, the general process involves referencing the programmed tool information, checking the tool table, and coordinating with the ATC to select and install the appropriate tool for the machining operation.
How does the CNC control system determine the tool length offsets for accurate machining?
The CNC control system determines tool length offsets to achieve accurate machining by using various methods and techniques. The specific method employed can depend on the capabilities of the CNC system and the machining requirements.
Here are a few common approaches:
Manual Entry: In some cases, the tool length offsets are manually entered into the CNC control system by the operator or programmer. This involves measuring the length of each tool and inputting the values into the control system’s tool table. The operator must ensure that the measurements are precise and updated whenever tool changes or adjustments are made.
Tool Length Measurement: Some CNC systems incorporate automatic or semi-automatic tool length measurement features. This may involve using a tool length measuring device, such as a tool presetter or a touch probe, to measure the length of the tool accurately. The measured values are then automatically entered into the control system’s tool table.
Probing and Tool Length Compensation: CNC systems equipped with probing capabilities can use touch probes to measure the actual length of the tool while it is installed in the spindle. The control system compares the measured length with the expected length stored in the tool table and calculates any necessary tool length offsets. These offsets are applied during machining to compensate for tool length variations, ensuring accurate positioning and machining results.
Laser Tool Measurement: Advanced CNC systems may employ laser tool measurement devices that can precisely measure tool lengths and diameters. Laser measurement systems can provide highly accurate and automated tool length offset data to the control system.
Once the tool length offsets are determined, the CNC control system applies these offsets during machining to compensate for any variations in tool length. The control system adjusts the Z-axis position based on the calculated tool length offsets, ensuring that the programmed tool paths accurately reflect the actual position of the cutting tool.
It’s important to note that the availability and implementation of tool length offset methods can vary among different CNC systems and machine manufacturers. The specific procedures and functionalities for determining tool length offsets can be found in the CNC system’s documentation or programming manuals provided by the machine manufacturer.
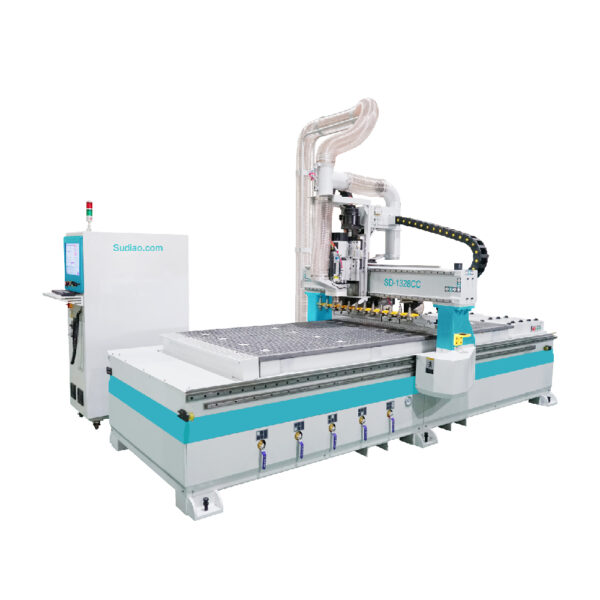
Comments are Disabled